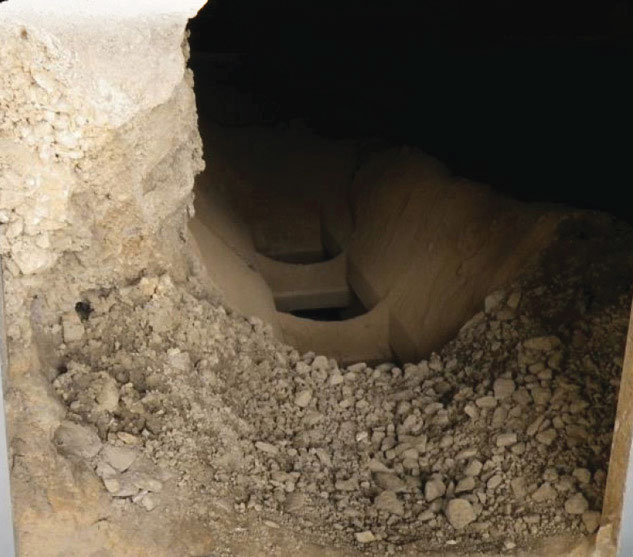
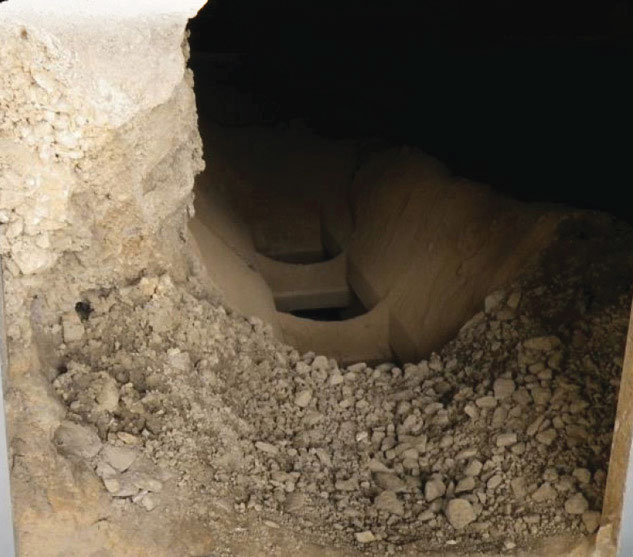
Falkville, AL- Mineral Processing and Material Handling employees constantly encounter situations with clogged chutes and conveyor systems, holes in the walls of equipment and product that won’t move. Costs vary depending on the volume and type of material being processed for such incidents, but all can create lost productivity and operational inefficiency. Regardless of the facility, personal safety is seen as an equal cost to everyone. This aspect is the most important and the impact of ensuring people’s safety is becoming costlier.
Operators in Mining and Mineral processing facilities must deal with people climbing into chutes to unclog material blockage. Confined spaces, lock-out/lock-off protocols and the associated permitting and authorization also makes the need for the correct chute and transfer point lining systems even more important.
Valley Rubber and its range of Inflatable Wear Liner Systems have helped resolve many of these problems for years. Recently in copper mines in Chile and gold mines in the USA, Valley Rubber’s Inflatable Liner Systems were installed, saving hundreds of hours in lost production and, at times, millions of dollars in additional productivity. In cement and aggregate facilities throughout the USA, we have eliminated the need for entering confined spaces and improved air quality significantly by reducing dusting created from material impacts. (Photo Left: Before a Plugged floor in a screen undersize chute.)
A Chilean Tertiary Crusher Plant had employees removing screen buildup manually twice a day, which equaled 56 hours of downtime a month with a designated “high risk to the personnel”. Many loss-time injuries were registered due to using pressurized air lances. The workers also received shoulder injuries due to this strenuous activity. The operation installed Valley Rubber’s Inflatable Liners and experienced decreased downtime and production gains of approximately 448,800 tons per year due to clean transfer chutes with no buildup, which gave continuous operations to the facilities. Overall the liners increased the facility’s uptime by 7.5%.
A simple screen underflow chute can be the cause of blockage due to sticky material, just as the discharge chute from a small conveyor can initiate a shutdown due to impact and abrasion damage on a side wall. Bad engineering can also allow large and small material to fall long distances damaging conveyors and chutes alike due to the kinetic energy it develops and expels on the equipment and surrounding walls.
Valley Rubber can customize a wear system to deal with all these issues. Our Inflatable Liners cover areas large and small, in thicknesses up to 5”, with controller systems that allow many different inflation or vibration options day or night for any duration of time. Using Valley Rubber Inflatable Wear Liners has, in many cases, also removed the complexities of physically entering any chute or confined space to deal with problematic material flow. This is a significant advantage benefiting the health and safety of employees, not to mention the reduced EH&S burden on management during plant shut downs. (Photo Right: Inflatable Liner Demo Stand.)
The Valley Rubber Inflatable Wear Liners & Systems are so effective we guarantee their performance. Contact Valley Rubber at 1.256.784.5231 and see if we can help make your mineral processing facility safer, cleaner and more productive.