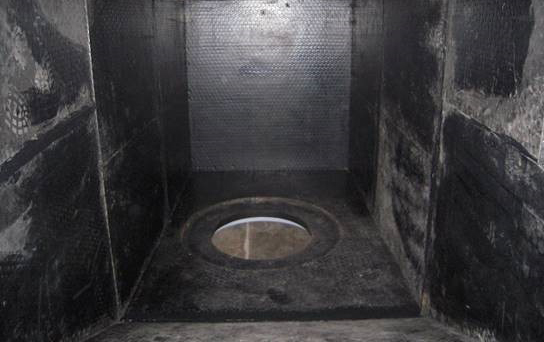
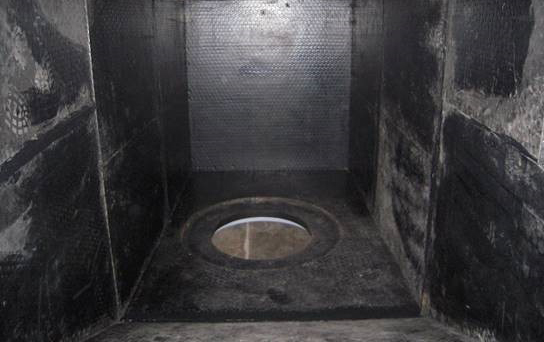
Falkville, AL- A mining company in Utah installed 1” vulcanized rubber in their underflow launders (which returns slurry from the Cyclone to the Ball Mill). This resulted in continual maintenance every eight weeks and included repairing and patching high wear areas. While rubber is more abrasion resistant than steel in the right application, ceramic is more abrasion resistant than rubber (although ceramic alone, without rubber, is often not the right solution).
As a result, the company installed Rubber-Ceramic Liners designed and manufactured by Valley Rubber and saw a dramatic increase in the liner’s wear life. (Photo: Launder Liners with Rubber-Ceramic held in place with internal magnets – no holes or hardware needed.)
The Solution
The entire launder was lined with 2” thick Rubber-Ceramic Liners which contained 1.25”x 1.25” ceramic cylinders embedded in V160, Valley Rubber’s proprietary 60 durometer rubber.
• Attachment method: Side liners were custom manufactured with integrated powerful magnets and bottom liners were pinned down by side liners.
• Designed for easily replaceable “donut liner” to be changed periodically in the field to extend life of the rest of the launder.
• Custom 1″ rubber ceramic liner for 28” OD x 64” tall discharge pipe.
• 20,000 gallons per minute, high wear and high impact situation.
Valley Rubber uses the best available technology to bond the ceramic and rubber together. A special coating is applied to the ceramics prior to molding at high temperatures and extreme pressure for an extended time creating a molecular bond between the ceramic and the rubber.
(Photo: The design was customized for the application and included fast and easy installation.)
This project’s success is due to the design, installation and quality of the Rubber-Ceramic Liners provided by Valley Rubber. The “donut liner” is replaced 1-2 times per year and can be completed during major shut downs without loss of production. The expectation for the Rubber-Ceramic Liners was three years, but after installing liners in all eight underflow launders in the circuit, preventative maintenance has been eliminated and the life of the project is now eight years and counting.